 |
 |
 |
 |
 |
 |
 |
 |
 |
 |
 |
 |
 |
 |
 |
 |
 |
 |
 |
 |
 |
 |
 |
|
|
|
|
|
|
|
|
|
|
|
|
|
|
|
|
|
|
|
|
|
|
|
|
|
|
|
|
|
Home Back to Machine Tool Illustrations Machine Tools For Sale & Wanted E-MAIL Tony@lathes.co.uk
Photographs of a little-used and very original 1905 Drummond B 31/2" Type B Headstock Type B Slide Rest Type B Tailstock Rare 4" Drummond Flat Bed Drummond Home Page Larger Drummonds Round Bed Drummond 1921 M Type 1925 M Type 1912 31/2" B Type Headstock Comparison Admiralty Model Little Goliath M-Type Photo Essay Rare early "double-height bed" Model Still in Use
The second version of the Drummond flat bed illustrated below was considerably modified with new bed, headstock and tailstock castings and redesigned headstock bearings. More details of these modifications and the machine's development can be found by following the hyperlinks above or looking here. A warning to those who restore old machine tools - when it's time to remove the old paint, be wary about using paint stripper. Old-time manufacturers were not so concerned about the quality of the castings they used - and had no qualms about applying a filler composed of lamp black, fiddler's rosin and iron filings or "borings" to cover up faults in the metal (an alternative was a mixture of sulphur, cast iron siftings and sal-ammoniac). The first mix, almost universally used, was known in the foundry trade as 'Beaumont's Egg' , possibly from a corruption of "beamontage", a filler used in the furniture trade. To hide minor faults in a casting Beaumont's Egg was run into blow holes and porous areas by melting it with a hot iron bar followed by rubbing down to make it almost undetectable. As an interesting aside the supplier of the cast-iron columns that collapsed in the Tay-bridge disaster used 'Beaumont's Egg' to cover his poor workmanship. Hence, the difference between a good foundry and a poor might have been the point at which a defect was accepted as being too large to fill, leading to a rejection of the casting. Unfortunately, early-filler soaks up paint stripper like a sponge - but then, being well absorbed into what are almost certainly porous castings, the metal refuses to let go; the result is that paint will not stick and the filler has to be mechanically removed - another hazardous operation. Be wary of using a sanding disc or powered wire brush - even sound casting were often lead filled to smooth out the imperfections - and you don't really want clouds of that flying around the workshop, do you?
|
|
|
|
|
|
|
|
 |
|
|
|
|
|
|
The first owner of this little used Drummond fitted a graduated handwheel to the single swivelling tool slide and a neatly made brass plate, precisely let into the end bracket, to carry a zero mark.
|
|
|
|
|
|
|
|
|
|
|
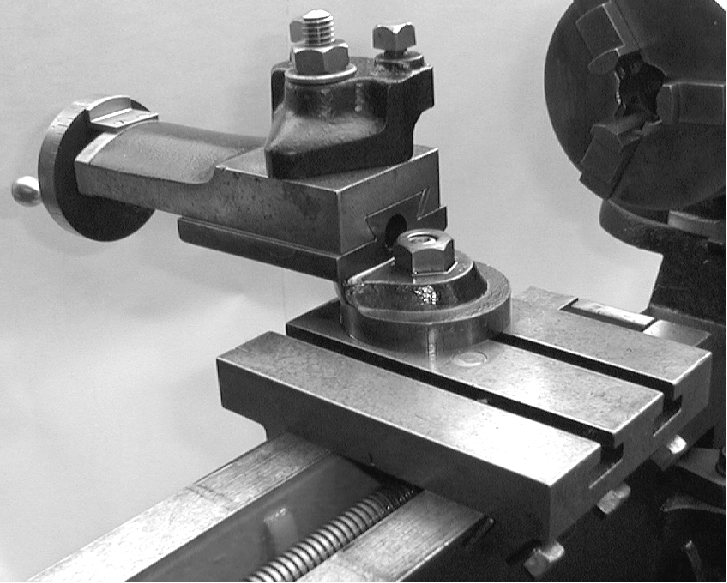 |
|
|
|
|
|
The tool slide, whilst undeniably elegant, was hardly the most rigid of structures with the mass cantilevered away at 90-degrees from the mounting boss and unsupported by any form of bracing
|
|
|
|
|
|
|
|
|
|
|
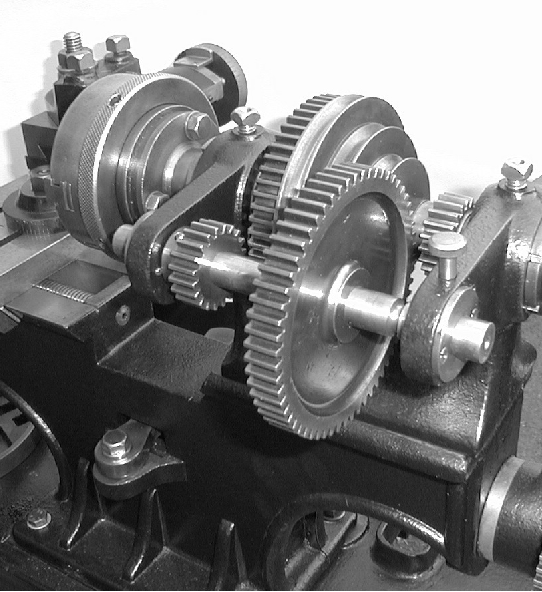 |
|
|
|
|
|
|
|
|
Rear of the headstock showing the sliding engagement for backgear and (on the back of the bed) the pivot for the leadscrew engagement dog clutch.
|
|
|
|
|
|
|
|
|
|
|
|
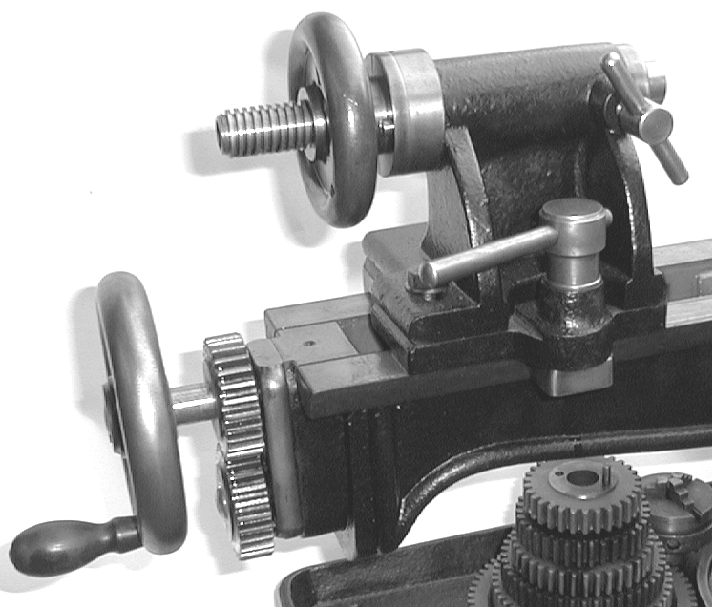 |
|
|
|
|
|
|
Drive from changewheels to carriage was by a dog-clutch-engaged shaft that passed beneath the bed and drove the leadscrew above it through exposed 1-to-1 gearing.
|
|
|
|
|
|
|
|
|
|
|
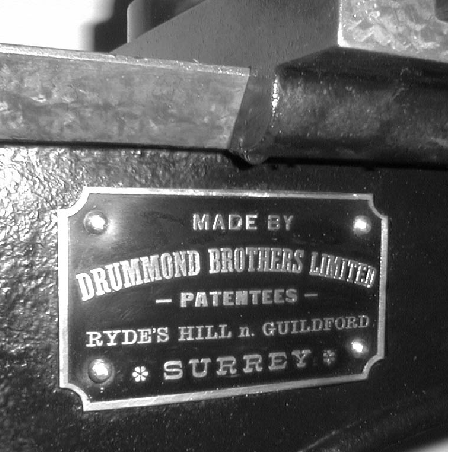 |
|
|
|
|
|
Maker's plates are often missing or damaged on early machines but this immaculate example shows that the lathe was built at the second home of Drummond, Ryde's Hill, near Guildford in Surrey. The original "frosting" marks are still visible on the bed.
|
|
|
|
|
|
|
|
|
|
|
|
|
|
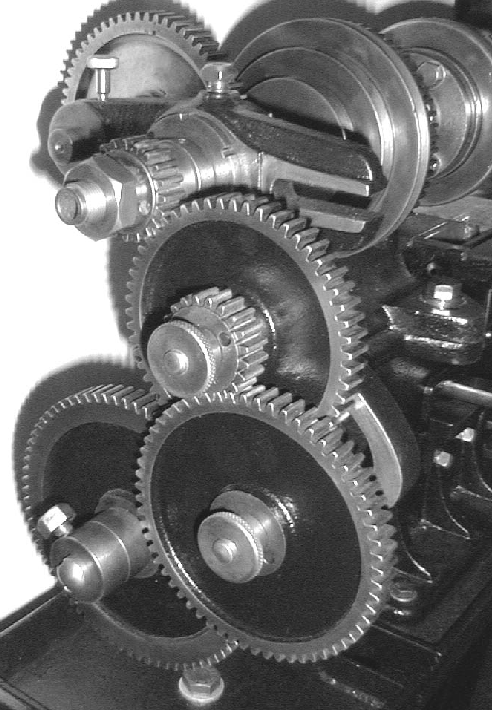 |
|
|
|
|
Compound reduction gearing set to give the highest possible numerical ratio between headstock spindle and leadscrew. For those unfamiliar with the technique, the largest gear is fitted on the leadscrew end, the second largest runs on the stud above whilst the third largest engages with the spindle gear. The smaller gears are arranged in a similar way: the smallest gear shares the uppermost stud on the changewheel arm with the second smallest (hidden in the picture on the inside of the lower stud) driving the leadscrew gear.
|
|
|
|
|
|
|
|
|
|