lathes.co.uk Home Page Machine Tool Archive Machine Tools For Sale & Wanted
E-MAIL tony@lathes.co.uk
Watch & Instrument Makers' Lathes
- some general notes -
Although there are various designs of watchmakers' lathe, some dating back to the late 1700s and including specialised models - for example "fiddle" lathes, "steel turns", Jacot, Swiss, Swiss Universal (also called the English Mandrel) Bottum and Dracip - more modern examples can generally be divided into two types: the lighter "Geneva" and heavier "WW". The "Geneva" can be recognised by a round bed, with a flat machined along the back for its full length and nearly always supported on a single foot. These lathes, invented in 1859 by Charles S. Moseley in the U.S.A., generally take a 6mm or 8mm collet and were designed only for lighter, very high-precision work. The "WW" (Webster-Whitcombe), is the more popular and versatile machine and also of American origin, from around 1889. The centre height of the WW was usually 50 mm, though very occasionally 65, 70 mm and other figures are encountered. The bed was of heavy construction, formed with a 37 mm-wide flat on the top and a 60-degree bevel along each edge, and carried a headstock spindle to accept 8, 10mm or 12mm collets. Larger than the WW type are what might be called "toolmakers' or "bench precision" lathes: these vary in size from the Schaublin 65 and 70 (the latter being the most popular and frequently-encountered machine in the professional watchmaker's workshop) to larger examples such as the Schaublin 102 and models by makers such as Boley, Lorch, Leinen, Stark, American Watch Tool Company, B.C. Ames, Wade, Pratt & Whitney, Rivett, Cataract, Hardinge, Elgin, Hjorth, Potter, Remington, Sloan & Chace and others. Whilst useful machines in a precision workshop these are outside the scope of this article.
There were dozens of brands of watchmakers' lathes and a lot of "badge engineering" went on. This was compounded by accessories being interchangeable between makes so it is entirely possible that a lathe has been "made up" from others. However, it's very unlikely that the bed, headstock and tailstock will be from different manufacturers; if they are, be wary.
You can see other examples of watch and instrument makers' lathes and their accessories here:
odkaz
http://www.lathes.co.uk/pultra
http://www.lathes.co.uk/boley/page3.html
http://www.lathes.co.uk/boley/page4.html
http://www.lathes.co.uk/boley/page5.html
http://www.lathes.co.uk/boley/page6.html
http://www.lathes.co.uk/boley/page7.html
http://www.lathes.co.uk/moseley
http://www.lathes.co.uk/bergeon
http://www.lathes.co.uk/btm
http://www.lathes.co.uk/levin (USA)
http://www.lathes.co.uk/derbyshire (USA)
http://www.lathes.co.uk/favorite
http://www.lathes.co.uk/ime
http://www.lathes.co.uk/lorchschmidt
http://www.lathes.co.uk/lorch
http://www.lathes.co.uk/derbyshire
http://www.lathes.co.uk/btm
http://www.lathes.co.uk/ime
http://www.lathes.co.uk/leinen
http://www.lathes.co.uk/rolls-royce
Continued below:
|
|
|
|
|
|
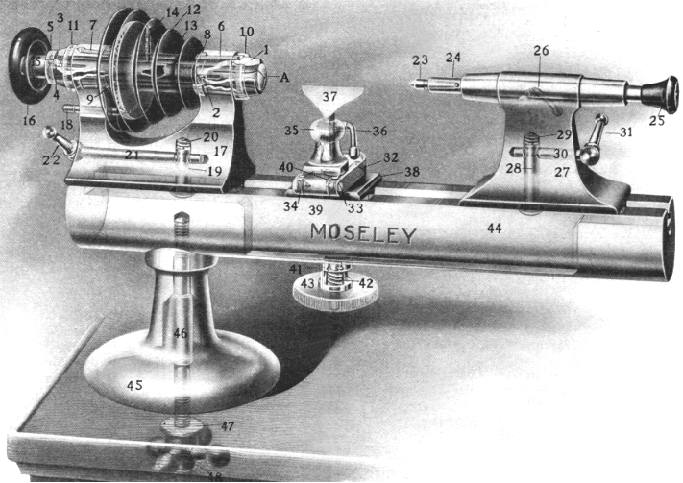 |
|
|
|
|
|
|
An early American-made Moseley lathe of the "WW" type with parts as annotated by the maker.
1. Headstock Spindle 2. Throat pin 3. Loose bearing 4. Loose bearing pin 5. Adjusting nut 6. Front bushing 7. Rear Bushing 8. Front inside shield 9. Rear inside shield 10. Front outside shield 11. Rear outside shield 12. Pulley 13. Pulley Hub 14. Pulley screw 15. Draw-in spindle 16. Draw-in spindle wheel 17. Frame 18. Index pin 19. Bolt 20. Spring 21. Eccentric 22. Lever 23. Pointed Centre 24. Spindle 25. Spindle Button 26. Spindle Binder 27. Frame 28. Bolt 29. Spring 30. Eccentric 31. Lever 32. Slide 33. Pivot Screw 34. Pivot Screw 35. Post 36. Lever 37. T graver rest 38. Shoe 39. Shoe bolt 40. Bolt pin 41. Bolt washer 42. Bolt spring 43. Bolt nut 44. Bed 45. Base 46. Base bolt 47. Bolt washer 48. Ball nut
|
|
|
|
|
|
|
|
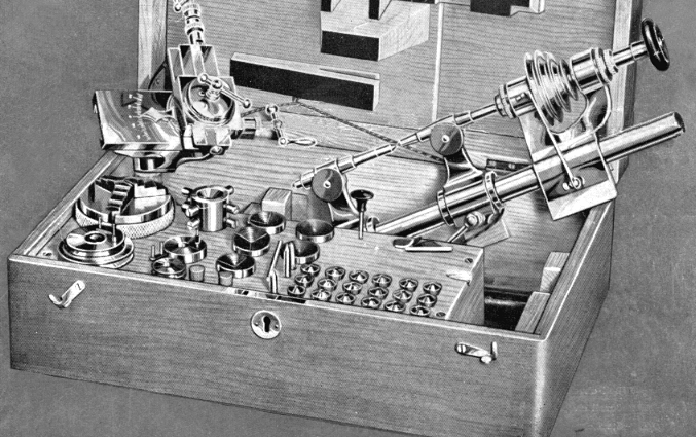 |
|
|
|
|
|
|
An English-made BTM "Geneva" pattern watchmakers' lathe (note the bar-like bed) complete in its maker's fitted wooden box with a range of useful accessories. The item top left in the box is the most valuable item - a compound slide rest, used to hold cutting tools and feed them to the work with the aid of two screw-controlled slides.
|
|
|
|
|
|
|
|
|
|
|
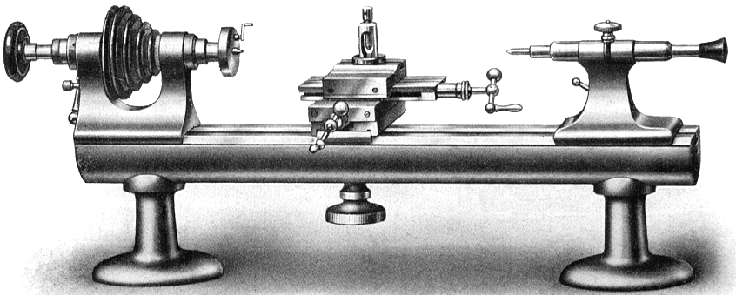 |
|
|
|
|
|
Boley Lathe No. 1b. A "WW" pattern lathe of a heavier pattern, admitting 230 mm between centres, and with feet at both end of the bed. On this model the compound slide was fitted as standard.
|
|
|
|
|
|
|
|
|
|
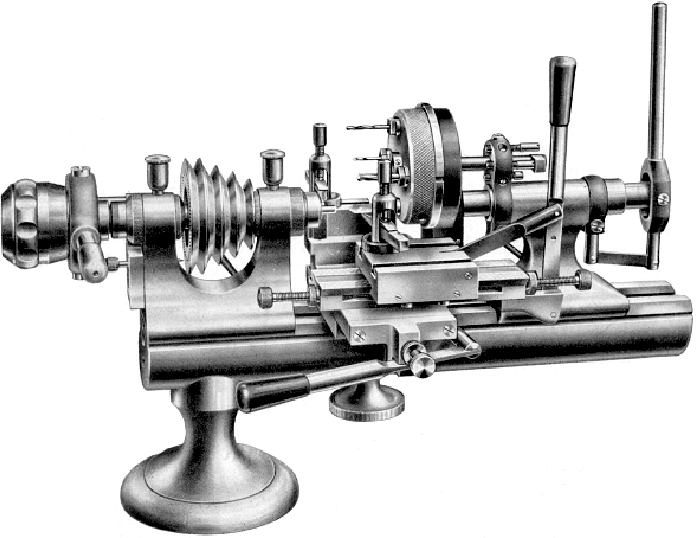 |
|
|
|
|
|
|
Another Boley but this time fitted for production work with quick-action levers fitted to the collet closer, compound slide and tailstock. The tailstock also has an indexing 6-station toolholder and the cross slide toolposts at front and back.
|
|
|
|
|
|
|
|
|
|
|
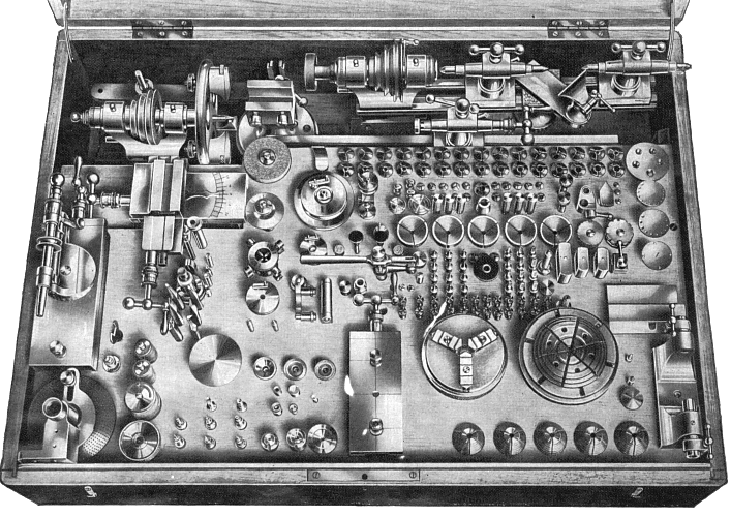 |
|
|
|
|
|
|
This is a later type of Boley & Leinen "Reform" lathe, manufactured from the early 1950s. The mouth-watering outfit was listed as the No. 77/X1V and contains virtually everything a skilled watch-repair man could wish for including, top left, a second headstock fitted with a permanently mounted and hence very accurately aligned faceplate.
|
|
|
|
|
|
|
|
|
|
|
|
Continued: Availability Watchmakers" or Instrument-makers' lathes can be very valuable, especially if they are in fine, original condition and complete with lots of accessories. Buying just a basic lathe with bed, headstock tailstock and T-type tool rest can be false economy - there are lots of these about, at attractively low prices, but the real value is in the extras that allow the lathe to be used as a miniature "machining centre" - as originally intended - to cut, for example, wheels (gears), mill small parts and hold tiny, awkwardly shaped mechanisms for repair and restoration. Because there is considerable competition for accessories, if your basic lathe has to be equipped one part at a time much time, effort and money will be expended - hence, if you can, find a fully-equipped lathe; this will be a much better investment and a lot easier for you, or your heirs, to sell. If you are looking for one of these machine I would strong recommend advertising for one. There are thousands sitting unused whose owners will never get round to advertising them - a "wanted" advertisement might just encourage them to get in touch: Accessories: Typically, the most valuable watchmakers' or instrument-makers' lathe would still be in its original wooden box with a wide range of equipment including as many of the following as possible: Compound slide rest - screw-feed or lever action Collets - a set of around 20 "Wire" (often called "split chucks"), Collets - "Wheel" type in a set of 5 or 6 Collets - "Ring Step" type in a set of 5 or 6 Box Chuck Chuck conventional 3-jaw Self-centring (sometimes called a "Universal Chuck") in ring-scroll (knurled ring round the outside) and key-operated models, Chuck conventional 4-jaw Independent Cutting tools - as large a collection as possible The following "chucks" mounted on collets: Chucks - balance Chucks - box type with screws through the body to hold jobs Chucks - brass split type (sometimes called jewel type) to fit inside larger steel collets Chucks - button or crown usually in sets of 10 Chucks - carrier for driving work between centres Chucks - circular-saw type Chucks - emery wheel Chucks - lantern in bronze or steel, Chucks - wax Chucks - wood screw Chucks - wood turning Compound Slide Rest Drill chuck for headstock or tailstock use Drilling plates - self-centring Drive Plate Eye glass on adjustable holder Fixed steady Jacot Drum Lapping attachment Pivoting attachment Saw table Sinking tools "Mandrel" - this has the appearance of a spare headstock with a "faceplate" attached and is used for super-precision work Micrometer-adjustable boring head Milling and Grinding Spindle, Pivot polisher Pivoting attachment Roller rest in single or double-wheel types Rose cutters Screwcutting Attachment with a set of Changewheels Sinking tools T-rest - the basic device to rest a tool against. Available in standard and tip-over types Tailstock chucks - also known as "drill stocks" and available with flat heads, V heads and chuck type Turning arbors Topping or "rounding up" tool Two types of Tailstock (sliding spindle and a lever-feed spindle), Tip-over or simple sliding T-shaped Hand-rest, Universal Faceplate and Pump Centre, Vertical milling Slide, Wheel-cutting attachment with division plate (to cut what the laymen would call gears but which are known to the watchmaker as "wheels"). Drive systems Even when fully equipped it is not unusual to find that a watchmaker's lathe has no drive system or even motor. However, this is rarely a problem for the easiest and cheapest solution is to use either the motor from a sewing machine or, preferably, a proper "Parvalux" unit - the latter available in 1-phase, 3-phase and DC types with speed ranges spanning 0.2 to 10,000 r.p.m. The motor can be bolted in place behind the headstock and driven by a special Swiss-made round plastic belt that can be flipped easily from pulley groove to pulley grove, there being no need to make up the type of hinged countershaft that a larger lathe would need. The writer can supply Parvalux motors their controller and the special belting Handbooks Unfortunately no maker of a watch lathes has ever offered a proper handbook for their products but, happily, there is an excellent hard-back book available that does the same job: "The Watchmakers' Lathe". This is a long-established publication and, because most of these lathes were built along the same lines, and use almost identical accessories, the book is able to give precise instructions that apply to all types. UK post-paid delivery: £18.75 EU post-paid delivery: £19.75 World-wide air-mail delivery: £26 (about US$67) email to order
Manufacturers and Brands Genuinely high-quality Watchmakers' lathes were manufactured and branded by, amongst others: Accro Adams George American Watch Company (C. S. Moseley-designed lathe circa 1859) American Watch Company (A. Webster-designed lathe circa 1859/60) American Watch Tool Company (Webster-Whiitcomb improved-design lathe of 1889 - the WW model) Ames ARS Bergeon Boley Boley-Leinen Boston Watch Company (C. S. Moseley-designed lathe circa 1858) Bottum Boydon B.T.M. Cataract (Hardinge) C.L.H. Coronet Derbyshire Dracup E.H.J. (E. H. Jones machinery dealers and commissioners) E.M.E. Favorite Gamma Gem (Gem Glorious) Gentil (Star Lathes, Switzerland) George Adams (re-branded Boley and Lorch, etc. and cheaper imitations under his own label) Hardinge (Cataract) Hammel, Riglander & Co. Hopkins IME Jones (J & T Jones UK) Lampert (U.S.A.) Lanco (Lane Cove) Leinen Levin Lorch (Lorch Schmidt) Manhora Mansfield Marshall Moseley Nordan Ohio Paulson Peerless Perton Precista Pultra Reliance Rivett Schaublin Schmidt Scomea (Société Commerciale d'Outillage et de Mécanique d'Aviation) Simplex Sloan & Chace Star (R. Gentil & Co. Company of La Brevine in Switzerland) Stark Steiner Swan Taylor T.C.M. Waltham Webster Webster-Whitcombe (WW) Whitcombe Wiskum Wolf, Jahn Some of these are featured in the Machine Tool Archive
|
|
|
|
|
|
|
|
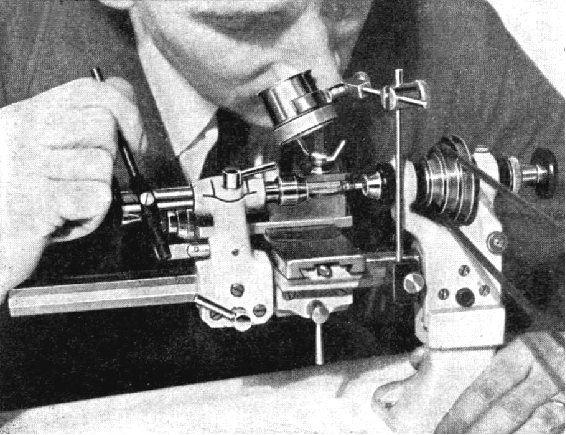 |
|
|
|
|
A Swiss-made Bergeon Model C of the "Geneva" type. This example is fitted with a compound slide rest to hold the cutting tool, a lever-action tailstock and, to assist with very small work, a magnifying glass held on an articulated arm
|
|
|
|
|
|
|